When Moisture In Your Building Is Costing You, Here’s How To Take Action
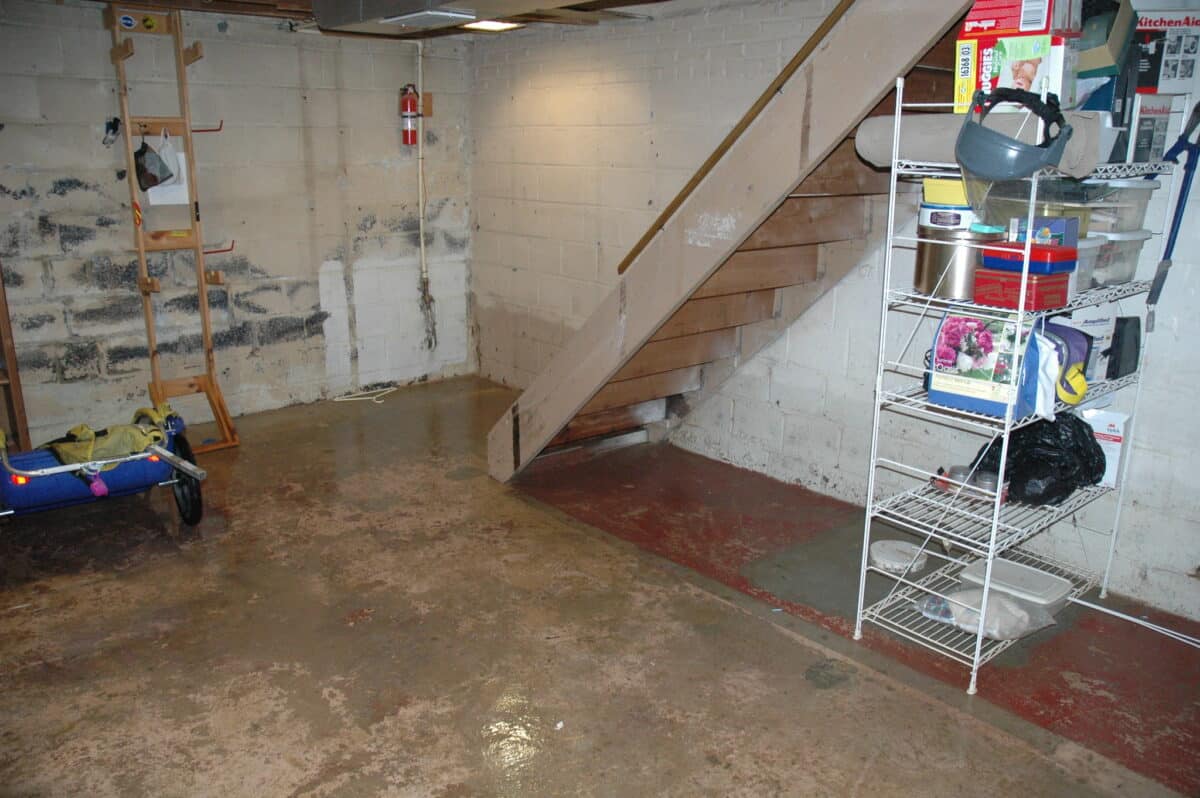
Moisture problems in buildings can lead to significant issues, from structural damage to health hazards like mold growth. To prevent these problems from escalating, it’s crucial to understand when and how to moisture test. Here’s a detailed guide on moisture testing, its importance, and the methods used.
When Should I Moisture Test?
Typically, moisture testing is necessary when there is a potential water intrusion event. For example, during new construction, concrete floors will release moisture into the building during the normal concrete curing process. Depending on the type of mixture, some curing times can exceed 30 days. As a precautionary measure, it is prudent to measure the moisture content prior to completing the finishes to eliminate the possibility of impacting other building materials with moisture, which can result in mold growth.
Water intrusion events can result from natural disasters, such as floods. Structural issues, such as a plumbing leak or extensive water use in certain areas of a building, like bathrooms and kitchens, can also lead to water intrusion events, window leaks or blocked weep holes, roof leaks, and fire suppression leaks. Also, seasonal changes, especially in areas prone to heavy rains or high humidity, can also prompt the need for moisture testing.
Moisture Testing in Concrete and Other Building Materials
It is important to moisture test for excessive moisture in an indoor environment to minimize the potential for building material damage and the proliferation of microbial growth. Excessive moisture can accumulate from many different water sources in a building, including but not limited to:
- Faulty fire sprinklers: These systems can leak or release water accidentally, contributing to unexpected moisture.
- Bathrooms, laundry rooms, and other areas where moisture collects: Inadequate ventilation can lead to condensation and increased humidity levels.
- Leaks in water transport mechanisms: Kitchen pipes, plumbing systems, and other water-carrying infrastructure can develop leaks that introduce moisture into building materials.
- Other indoor and outdoor sources: Humidity from the environment or improper water drainage around the building can contribute to indoor moisture issues.
- Faulty vapor barriers on concrete subfloors: Vapor barriers are designed to prevent moisture from penetrating the subfloor, but if these barriers are compromised, moisture can seep through a concrete subfloor and cause damage.
Advanced Moisture Mapping Techniques for Buildings
When building owners suspect moisture intrusion, conducting an accurate moisture mapping can help identify the source of intrusion and mitigate potential damage. Combining an infrared thermal camera with a moisture meter offers a comprehensive solution.
The infrared thermal camera is adept at detecting surface temperature variations, which often indicate moisture presence. Moist areas typically appear cooler on the infrared spectrum due to evaporation, allowing for a non-invasive, broad sweep of the suspected areas. Once these potential moisture spots are identified, a moisture meter is employed to confirm the findings. The moisture meter provides precise, quantitative data about the moisture levels, ensuring that the diagnosis is accurate.
This dual-method approach not only enhances the reliability of moisture detection but also aids in pinpointing the exact location and extent of the intrusion. Early and precise detection through this technique helps in addressing the issue promptly, preventing further structural damage, mold growth, and associated health risks. Building owners can then implement targeted remediation strategies, ensuring the longevity and safety of the building. Using these advanced tools in tandem exemplifies a proactive approach to maintaining building integrity and indoor air quality.
During the construction process, testing for moisture in concrete slabs, otherwise known as moisture vapor emission testing, is essential. It should be performed on concrete regardless of its apparent condition. Concrete slabs should be tested regardless of age or grade level, whether on grade, above grade, or below grade. From the penthouse of a building to the basement, the concrete should be tested. Proper moisture testing of the slab will determine the moisture content and potential emissions into a building space. The findings could reveal subfloor conditions that allow you to source the correct type of floor covering that is needed. This will help you avoid future issues such as delamination of VFT or sheet vinyl and, more importantly, mold growth on carpet padding and carpeting.
Two Common Methods for Moisture Testing
Two common methods for moisture testing can provide valuable information and understanding of the slab’s moisture condition.
- ASTM F 2170: The American Society of Testing and Methods (ASTM) Standard ASTM F 2170 is a standard test for measuring the relative humidity in concrete floor slabs using In Situ probes. This method involves placing probes into the concrete to measure the internal humidity levels, giving an accurate reading of the slab’s moisture condition.
- ASTM F 1869: Another standard test method is ASTM F 1869, which measures the vapor emission rate of concrete slabs using Anhydrous Calcium Chloride. This test involves placing a sealed dish of calcium chloride on the concrete surface and measuring the amount of moisture absorbed over a specific period. This method provides information about the surface moisture emissions of the concrete.
Importance of Professional Moisture Testing
While there are DIY moisture testing kits available, professional moisture testing is recommended for accurate and reliable results. Omega Environmental Services, Inc. has qualified and certified professionals, including Certified Industrial Hygienists, Professional Engineers, Geologists, Certified Asbestos Consultants, Certified Lead Professionals, and Toxicologists, who have the expertise to assist businesses in assessing and managing their hazardous materials. These professionals use state-of-the-art equipment and methodologies to ensure precise moisture readings and provide recommendations based on the findings.
The Impact of Excessive Moisture
Excessive moisture in buildings can lead to several serious issues, including:
- Structural Damage: Moisture can weaken structural elements, leading to compromised integrity of the building.
- Mold Growth: Mold thrives in moist environments and can cause health problems such as allergies, respiratory issues, and infections.
- Damage to Finishes: Moisture can cause finishes such as paint, wallpaper, and flooring to deteriorate, leading to costly repairs and replacements.
- Poor Indoor Air Quality: Excessive moisture can contribute to poor indoor air quality, affecting the health and comfort of occupants.
- Increased Maintenance Costs: Addressing moisture-related issues can be costly and time-consuming, especially if not detected early.
Preventive Measures for Excessive Moisture In Buildings
Preventing moisture problems in buildings involves a combination of proper design, construction practices, and maintenance. Here are some preventive measures to consider:
- Proper Ventilation: Ensure adequate ventilation in moisture-prone areas, such as bathrooms, kitchens, and laundry rooms. Use exhaust fans to reduce humidity levels.
- Waterproofing: Apply waterproofing measures to areas exposed to water, such as basements, foundations, walls, and roofs. Use vapor barriers and sealants to prevent moisture infiltration.
- Regular Inspections: Regularly inspect the building’s plumbing, HVAC systems, and other water-related infrastructure to identify and address leaks or potential issues.
- Moisture Monitoring: Install moisture monitoring systems to detect changes in moisture levels and address them promptly.
- Drainage Systems: Facilitate proper drainage around the building to prevent water from accumulating near the foundation and sill plate. Use gutters, downspouts, and grading to direct water away from the building.
Is There Moisture in Your Building? Trust Omega’s Experts
If not addressed promptly, moisture problems in buildings can lead to significant damage and health hazards. Moisture testing is a crucial step in identifying and mitigating these issues. By understanding the importance of moisture testing, the methods used, and the preventive measures, building owners and managers can protect their investments and ensure a safe and healthy environment for occupants.
Omega Environmental Services offers expert moisture testing and consulting services to help businesses manage moisture-related issues. With a team of qualified professionals and advanced testing methodologies, we provide accurate and reliable results, helping clients make informed decisions and take preventive actions to safeguard their buildings.
Investing in moisture testing and preventive measures can save significant costs in repairs, improve indoor air quality, and maintain the structural integrity of buildings. Don’t let moisture problems escalate – take action today to protect your property and ensure a healthy environment for all.
FAQ: When Moisture in Your Building Is Costing You, Here’s How To Take Action
1. When should I test my building for moisture? Testing for moisture is crucial during new construction, especially in concrete curing processes that can exceed 30 days. It’s also necessary after water intrusion events such as floods, plumbing leaks, or seasonal changes that cause high humidity. Regular testing helps prevent damage and mold growth.
2. What are the common methods for moisture testing in buildings? Two common methods are ASTM F 2170, which measures relative humidity in concrete slabs using In Situ probes, and ASTM F 1869, which measures the vapor emission rate using Anhydrous Calcium Chloride. Both methods provide valuable insights into the moisture conditions of building materials.
3. Why is professional moisture testing important? Professional testing facilitates accurate and reliable results, critical for effective remediation. Certified professionals like Omega use advanced equipment and methodologies to assess moisture levels and provide tailored recommendations, helping to prevent structural damage, mold growth, and poor indoor air quality.