Moisture Management for Construction in Soggy Times
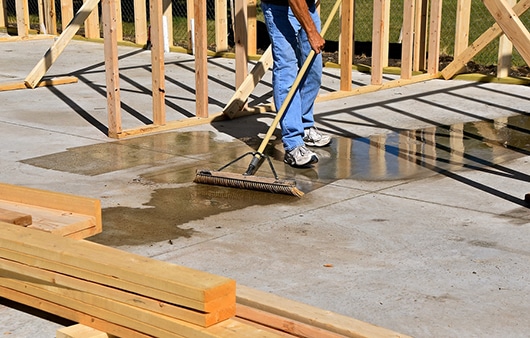
A soggy few weeks in Southern California following a very dry winter season has heightened the moisture management challenges for property developers and construction companies trying to keep their projects dry.
Moisture management on construction sites is critical for both environmental safety and a successful build. Moisture problems can lead to expensive delays and the added cost of replacing water or mold-impacted materials if left unchecked.
With a flood of late-season rain intersecting busy construction schedules, Southern California project managers have had more than the usual share of moisture challenges on their job sites.
But the weather is far from the only source of moisture trouble.
Not long ago Omega was called in to help mitigate a potentially disastrous water mishap that occurred when our client discovered an incorrectly installed valve behind a shower wall. The resulting leak affected 300 units. While a subcontractor was left with more than $1 million in repair work, it would have been much worse without swift action. Building materials such as drywall, wood, carpeting, and other flooring types typically begin absorbing moisture as soon as they are impacted by water. Once damp or wet, mold can begin to grow on drywall and under flooring material in as little as 24 to 48 hours, according to the EPA.
Consistent monitoring, proactive management and timely remediation are critical.
Identifying Moisture Issues that Can Soak Your Construction Budget
Some common sources of construction site moisture include:
- Weather: Heavy rains, or rain that occurs before windows are installed
- Leaky roofing
- Fire sprinklers that have been accidentally set off
- Improperly installed plumbing or pipe breaks
- Improperly installed landscape sprinklers
- High indoor humidity without proper ventilation
- Drywall that is installed before concrete is poured can “wick up” moisture during the concrete curing process
Water intrusion events can happen at any time during the construction process. If you are concerned about potential water damage, an onsite environmental assessment can make the difference between a little problem and a soaking.
Suspected moisture intrusion requires a thorough assessment that includes inspection for signs of water staining, temperature differentials using infrared technology, elevated moisture, and suspect mold growth (SMG) in any building materials throughout the site.
Remediating and Preventing Moisture Damage in the Construction Process
Once water damage has been identified, it’s important to act as quickly as possible.
In less severe cases, remediation might mean disinfecting and cleaning building materials and drying the area. Worst-case scenarios require removal and replacement of drywall, wooden structures, and flooring, sometimes in large areas of construction.
Newly poured concrete without adequate ventilation to cure properly can create humidity and moisture that quickly spreads to drywall. Omega’s industrial hygienists have assessed a project where moisture from uncured concrete left 65 hotel rooms with flooring and drywall that had to be removed. If drywall is in place before concrete is poured, you have a week or less before moisture from any uncured sections is likely to be absorbed into drywall.
Effective moisture management includes preventative measures such as:
- Moisture mapping
- Planned construction sequence to avoid introducing moisture after drywall and other vulnerable materials are in place
- Periodic moisture assessment of concrete and drywall
- Mold and moisture assessment following any known or suspected moisture intrusion
- Testing fire sprinklers, plumbing, and roof systems for leaks
- Spot checks for discoloration, texture changes, and decay
- Regular assessment of indoor relative humidity and temperature
- Development of proactive moisture and mold growth control strategies
Moisture Management Expertise
Omega offers a wide range of cost-effective environmental assessment and remediation services for construction, demolition, and renovation, including mold and moisture assessment and management. Our certified personnel and industrial hygienists have deep expertise in water damage investigations to identify and remediate any source of damage or mold and mildew contamination and get your project back on track.
Give us a call or click on the link below to learn more about the best moisture management practices for your project.
Contact Us to Learn More About Moisture Management for Construction