Construction Site Dust Monitoring Keeps Projects Safe and Compliant
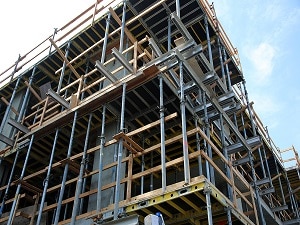
Construction site hazards can be obvious and dramatic: falls from ladders and rooftops, slips on unstable surfaces, blows from heavy machinery, chemical and electrical risks…
But one of the most dangerous threats lurking in construction sites is far more insidious: dust.
Dust – generated from concrete, rock, mortar, metal and more when it is drilled, ground, crushed, blasted or hauled – isn’t just a nuisance; improperly controlled, it can be toxic and even fatal.
“There is so much construction and renovation-related work going on throughout the state. It can be a real challenge for construction managers to keep up with the need for daily onsite monitoring of construction dust.” – Omega President and Project Director Steve Rosas.
For a hazard so small it may seem inconsequential, dust poses so serious a threat to those who inhale it that a slew of state and federal regulations exists to control its spread at construction sites.
Developers, builders, and contractors must maintain regulatory compliance and ensure that construction dust is closely monitored and managed.
Construction Dust Dangers
Once airborne, dust can cause a number of respiratory diseases including asthma, pneumonitis, bronchitis, silicosis, and lung cancer.
Silicosis, a serious and irreversible lung disease caused by inhaling crystalline silica (or silica dust), is one of the most common construction-related respiratory illness. Silica dust is found in concrete, brick, stone, quartz and mortar and created when those substances are crushed, grated or sawed. Individual particles are at least 100 times smaller than sand, according to the Occupational Safety and Health Administration (OSHA). When poorly controlled, clouds of those particles are easy to breathe in.
Prolonged exposure to silica dust can cause lung scarring and severe shortness of breath. According to the National Institute for Occupational Safety & Health (NIOSH), over 200 U.S. workers die from silicosis each year and hundreds more become disabled.
Construction Dust Regulatory Standards
OSHA estimates that over 2 million U.S. workers are exposed to silica dust while on the job. Millions more – who live or work near construction sites – have the potential for exposure.
Federal standards require employers to monitor, contain and limit exposure to dust and provide respirators, dust suppression among other requirements.
At a state level, regulations like California’s air quality standards establish additional safeguards, like the prohibition of visible emissions that could impact neighboring properties.
What to Do About Construction Dust
If you are a developer or contractor, complying with regulations around construction dust can mean using water suppression to keep dust down and/or employing engineering controls like filtration, negative air pressure and ventilation adjustment for indoor work environments. Primarily dust suppression using water and worksite perimeter dust monitoring is performed for outdoor environments.
For indoor projects, it is also wise to have an Industrial Hygiene / Indoor Air Quality assessment to ensure that dust levels are under control.
But, because each project is different, the best practice is to partner with an environmental management and consulting firm with the expertise to advise on the most effective solutions for your needs and to monitor your efforts.
Let Omega Environmental be Your Guide
Omega Environmental has over two decades of experience providing tailored solutions for the management of hazardous materials for clients that includes major universities, airports, developers and more. Our team of experienced toxicologists, microbiologists and certified industrial hygienists have expert-level knowledge of how to control dust on construction sites and deep experience in the assessment and monitoring of such efforts throughout construction projects.
“There is so much construction and renovation-related work going on throughout the state,” said Omega President and Project Director Steve Rosas. “It can be a real challenge for construction managers to keep up with the need for daily onsite monitoring of construction dust. We come in and do the initial hazmat assessment and may get involved in abatement. During construction, we support the dust monitoring during working hours to ensure the safety and compliance of the project.”
A selection of dust monitoring projects Omega has managed include:
- A renovation at Bachelor Hall at the University of California at Riverside. Residents remained in place, so dust monitoring and mitigation controls were established for the interior and exterior of the building. This ensured that dust did not travel from the construction area into occupied areas. Protocols and procedures were outlined so occupants would not be exposed to elevated concentrations of dust or asbestos.
- A demolition project at the University of California at Irvine. Dust monitoring was employed on the perimeter of the project to avoid impacting neighboring housing.
- Construction on terminals B and C of John Wayne Airport in Orange County. High-tech and low-cost fenceline monitoring was used to ensure that no visible emissions impacted office buildings across the street.
- A demolition and renovation project at a large-scale building in Los Angeles with retail, office and an on-site, occupied daycare center. Engineering controls were put into place and indoor air quality was assessed daily.
By planning ahead and partnering with Omega, our clients could keep their projects on track safely and compliantly – confident that workers, occupants and neighboring structures were not at risk of exposure to uncontrolled dust.
To learn more about the benefits of expert dust monitoring and assessment for your next construction project, contact our team of experts.