A New Beginning for Army Training Center
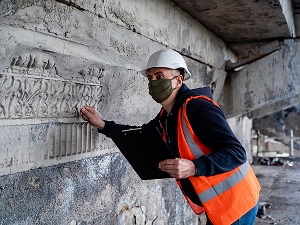
Built in 1943 during the height of WWII, Camp Parks Training Center in Dublin, Calif., lies just east of San Francisco. In its prime, this training center and air force base could house over 20,000 military personnel. Today, the base functions as a semi-active mobilization and training center to be used in times of war or natural disaster.
The U.S. Army sold part of the property to developers in exchange for building renovations needed for the active locations on the base. But with structures dating back to WWII, the developers required an experienced demolition partner to mitigate potential hazardous materials found on the site.
Asbestos, lead, and polychlorinated biphenyls (PCBs) were just a few of the environmental concerns facing the developers hoping to turn this former military site into a master-planned community complete with residential, retail, and commercial spaces.
Hazardous Building Materials on Historical Sites
Historic buildings – particularly those built between the 1930s and 1980s – are likely to have been constructed with building materials containing high levels of toxic materials, such as asbestos. While the use of these materials in construction has significantly declined over the last century, asbestos was widely used to fireproof everything from roofs to electrical appliances.
Lead, PCBs, and other harmful substances can also be found in historic buildings. If not handled correctly, demolition of hazardous building materials can cause these contaminants to become airborne or released into the environment, risking the health of demolition workers and nearby building occupants.
The handling and disposal of hazardous materials such as asbestos, lead, and PCBs must follow specific federal, state, and local regulations for the safety of both civilians and the environment.
Proper Handling and Disposal of Hazardous Materials
Before renovation of existing buildings could occur, the Camp Parks site had to be tested for suspect hazardous building materials in need of removal and proper disposal. For the developers, this meant finding a partner whose expertise could guide them through the next steps of demolition.
With more than 25 years of experience in environmental management, Omega assisted in determining the safety of the sites. Our team of industry experts completed a full pre-demolition assessment of more than 20 buildings on the site, testing for and removing hazardous materials in wall systems, flooring, insulation, ducting, roofing, and electrical transformers.
“(Omega) went above and beyond.Whenever I needed something, they got it done in a quick manner so that I could move forward.” –Camp Parks renovation Project Manager
In addition to asbestos and lead surveys, the Omega team performed sampling of nine pole-mounted transformers on the site that had been stored for proper disposal. The interior mineral oil contents were analyzed for hazardous constituents, including PCBs. Additionally, Omega assessed the areas surrounding the former locations of the transformer units to ensure there was no visible indication of spilled or leaked transformer oil near the buildings.
Over two years, Omega worked closely with the developer to maintain safety throughout the entire process of demolishing and remodeling the historical structures on site.
An Environmental Partner for Safety and Compliance
Due to strict regulations from the California Air Resources Board, the developer had to provide regular compliance reports with the help of Omega’s team. The simultaneous demolition and renovation of on-site structures meant the developer was on a tight deadline. As new buildings were completed, the occupants of the army base moved out of the old buildings that would soon be demolished. Omega’s involvement was therefore crucial in maintaining both the project’s scope and timeline.
“(Omega) went above and beyond,” the project manager said. “Whenever I needed something, they got it done in a quick manner so that I could move forward.”
Even when working with short turnarounds, the project manager felt that Omega was able to provide timely, full reports.
“They have good accountability,” noted the project manager. “They were really good to work with, and that’s why we’ve continued to work with them.”
As a full-service environmental management and hazardous materials consulting firm, Omega prides itself on responsiveness, reliability, and efficacy for regulatory compliance. With a diverse team of industry professionals, Omega provides a full suite of environmental services, from assessment to decontamination.
To learn more about Omega’s site assessments and remediation services, click the link below.