How to Conduct a Hazardous Materials Assessment in Buildings
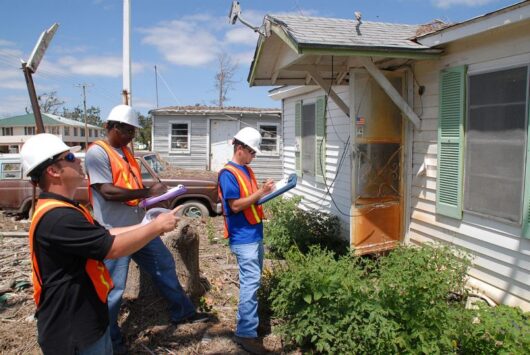
Facilitating Building Safety with a Hazardous Materials Assessment
A hazardous building materials assessment is critical for identifying unsafe materials like asbestos, lead, mercury, and polychlorinated biphenyls (PCBs) before starting any renovation or demolition project. By conducting this assessment, you address key concerns for regulatory compliance, safety, and environmental protection.
Quick overview:
- Identify hazardous materials (asbestos, lead, mercury, PCBs, etc.).
- Evaluate environmental contamination (soil, groundwater).
- Ensure compliance with local, state, and federal regulations.
- Assess risks and plan remediation.
- Estimate project costs and protect against liabilities.
Understanding the importance of assessing hazardous materials can save significant costs and time, prevent health risks, and avoid legal issues. Regulatory bodies such as the EPA and OSHA enforce strict guidelines to manage these materials safely. Compliance with these rules is not just about avoiding fines—it’s about fostering a safe and healthy environment.
I’m Steve Rosas. With over 26 years of experience in the Architectural, Engineering, and Construction (A/E/C) industry, I specialize in hazardous building materials assessment. My focus is on developing effective strategies for identifying and mitigating environmental hazards to ensure your projects run smoothly and safely.
Understanding Hazardous Building Materials
What is a Hazardous Materials Assessment?
A Hazardous Materials Assessment (HazMat Assessment) is a comprehensive evaluation of a building to identify materials that may pose health and environmental risks. This assessment is crucial before any renovation or demolition project to protect the safety of workers, building occupants, and the surrounding environment.
Key Components of a Hazardous Materials Assessment:
- Visual Inspections: Experts visually inspect the building for potential hazards.
- Sampling: Materials suspected of containing hazardous substances are sampled and analyzed in a lab.
- Written Report: A detailed report outlines the findings and provides recommendations for mitigation.
Common Hazardous Materials in Construction
Asbestos
Asbestos is a group of fibrous minerals once popular for their heat resistance and insulating properties. Commonly found in older buildings, asbestos can be present in:
- Insulation
- Floor tiles
- Roofing materials
- Popcorn ceilings
When asbestos fibers become airborne and are inhaled, they can cause serious health issues such as mesothelioma, asbestosis, and lung cancer. According to the EPA, asbestos is considered a hazardous waste and must be properly managed and disposed of.
Lead
Manufacturers and builders used lead in paints, plumbing, and various building materials before its health risks were fully understood. Lead exposure, particularly from lead-based paints, can cause severe health problems, including developmental issues in children and cardiovascular problems in adults. The EPA’s lead-safe practices rule mandates that contractors follow specific work practices to prevent lead contamination during renovation activities.
Mercury
Certain types of electrical parts contain mercury, such as:
- Fluorescent lamps
- Thermostats
- Switches
A small mercury spill can be challenging to clean up and poses significant health risks. The EPA regulates mercury as a hazardous waste, requiring careful handling and disposal.
Polychlorinated Biphenyls (PCBs)
Synthetic chemicals used in various industrial applications can contains PCBs, such as:
- Electrical transformers
- Light ballasts
- Caulking
Although the U.S. government banned PCB production in 1979, they may still be present in older buildings. PCBs can leach into indoor air and contaminate surrounding materials, posing serious health risks.
Chlorofluorocarbons (CFCs)
The U.S. government now regulates the use of CFCs, once common in refrigeration and air conditioning systems, due to their ozone-depleting properties. Proper recovery and disposal of CFCs are essential to comply with environmental regulations and protect the ozone layer.
Radioactive Sources
Some building components, like smoke detectors and exit signs, contain low-level radioactive materials. These sources require specialized handling and disposal to prevent radiation exposure.
Health Hazards and Environmental Impact
Exposure to hazardous building materials can lead to severe health issues, including respiratory problems, cancer, and developmental disorders. Additionally, improper disposal of these materials can contaminate soil and groundwater, leading to long-term environmental damage.
By conducting a hazardous building materials assessment, you can identify and manage these risks effectively, ensuring a safe and compliant project.
In the next section, we’ll dig into the steps for conducting a hazardous building materials assessment, including planning, tools, and regulatory compliance.
Conducting a Hazardous Building Materials Assessment
Planning Your Assessment
Before diving into a hazardous building materials assessment, it’s crucial to have a solid plan. Proper planning ensures that the assessment is thorough and effective.
Survey Scope: Define the scope of your survey. Are you assessing an entire building or specific areas? Knowing the scope helps in allocating resources and time effectively.
Site-Specific Sampling: Identify areas hazardous materials are likely to be found. This could include older insulation, paint, flooring, and electrical components. Tailor your sampling strategy to the specific characteristics of the site.
Risk Analysis: Evaluate the potential risks associated with the identified hazardous materials.
Tools and Techniques for Assessment
Different hazardous materials require specific tools and techniques for proper identification and evaluation. Some key methods used in the assessment include:
Asbestos Survey:
- Visual Inspection: Look for materials that may contain asbestos, such as insulation and floor tiles.
- Sampling: Collect samples of suspect materials and send them to a lab for analysis.
- Air Monitoring: Measure airborne asbestos fibers to assess the risk of exposure.
Lead Survey:
- XRF Analyzers: Use handheld X-ray fluorescence analyzers to detect lead in paint and other materials.
- Dust Wipe Sampling: Collect dust samples from surfaces to check for lead contamination.
Mold Assessment:
- Moisture Meters: Measure moisture levels in walls and floors to identify areas prone to mold growth.
- Air Sampling: Collect air samples to detect mold spores and assess indoor air quality.
PCB Inspection:
- Visual Identification: Inspect electrical transformers, light ballasts, and caulking for signs of PCBs.
- Sampling: Collect samples of suspect materials and send them for laboratory analysis.
Regulatory Compliance and Safety Protocols
Compliance with regulations is a critical aspect of conducting a hazardous building materials assessment. Here are some key regulations and standards to keep in mind:
EPA Regulations: The Environmental Protection Agency (EPA) has specific guidelines for managing hazardous materials like asbestos, lead, mercury, and PCBs. For example, the EPA’s asbestos regulations under 40 CFR 61 require an inspection before any renovation or demolition activities.
OSHA Standards: The Occupational Safety and Health Administration (OSHA) sets permissible exposure limits (PELs) for hazardous materials. Employers must conduct initial exposure monitoring and implement control measures to protect workers.
Local Laws: State and local regulations often adopt federal standards but may also have stricter requirements. Always check with local authorities to ensure compliance with all applicable laws.
By following these steps and using the right tools, you can effectively conduct a hazardous building materials assessment. This will help you identify potential risks, comply with regulations, and ensure the safety of everyone involved.
In the next section, we’ll discuss managing and mitigating risks associated with hazardous materials, including removal, remediation, and safe disposal.
Managing and Mitigating Risks
When dealing with hazardous building materials, managing and mitigating risks is crucial. This involves safe removal, remediation, and disposal of hazardous substances like asbestos, lead, mercury, and PCBs.
Handling Asbestos and Lead
Asbestos:
- Abatement Techniques: Asbestos abatement involves removing or encapsulating asbestos-containing materials (ACMs). This must be done by certified professionals to prevent the release of asbestos fibers.
- Protective Measures: Workers should use personal protective equipment (PPE) such as respirators and protective suits. Work areas must be sealed off to prevent contamination.
- EPA Guidelines: The EPA requires notification 10 business days before any demolition. ACMs must be identified and removed before starting work. The Occupational Safety and Health Administration (OSHA) also mandates regular air monitoring to ensure safe levels of asbestos fibers.
Lead:
- Abatement Techniques: Lead paint can be removed by chemical stripping, wet sanding, or encapsulation. Each method has its pros and cons, depending on the material and location.
- Protective Measures: Workers should use PPE, including gloves, masks, and eye protection. Containment barriers should be set up to prevent the spread of lead dust.
- EPA Guidelines: The EPA’s Renovation, Repair, and Painting (RRP) Rule requires certification for contractors working with lead-based paint in homes, child care facilities, and schools built before 1978.
Dealing with Mercury and PCBs
Mercury:
- Cleanup Procedures: Mercury spills should be cleaned up using specialized kits to prevent vapor release. Spills larger than one pound must be reported to federal authorities.
- Disposal Requirements: Mercury-containing devices, such as fluorescent lamps and thermostats, should be recycled or disposed of at hazardous waste facilities.
- Safety Equipment: Use of mercury vapor analyzers and proper ventilation systems is essential during cleanup to monitor and control mercury levels.
PCBs:
- Inspection and Removal: PCBs can be found in electrical transformers, light ballasts, and caulking. These materials must be identified and removed by trained professionals.
- Disposal Requirements: PCB-containing materials must be disposed of according to the Toxic Substances Control Act (TSCA) regulations. This often involves incineration at EPA-approved facilities.
- Safety Equipment: Workers should use PPE and follow strict decontamination procedures to avoid exposure.
Innovative Practices for Hazard Management
Recycling and Reuse Technologies:
- Recycling: Many hazardous materials can be recycled. For example, mercury from fluorescent lamps can be recovered and reused.
- Reuse Technologies: Technologies that allow for the reuse of materials, such as decontaminating and repurposing lead-contaminated soil, help reduce waste.
Waste Minimization:
- LEED Green Guidelines: Following LEED Green guidelines can help minimize waste by promoting recycling and reuse. This not only reduces environmental impact but also lowers disposal costs.
- RCRA Waste Minimization: The Resource Conservation and Recovery Act (RCRA) encourages waste minimization practices to reduce the volume and toxicity of hazardous waste.
By following these practices, you can effectively manage and mitigate the risks associated with hazardous building materials. This ensures the safety of workers and occupants while complying with regulatory requirements.
In the next section, we’ll explore the importance of professional expertise in hazardous materials management and how certified professionals can provide comprehensive solutions.
Conclusion
Future Trends in Hazardous Materials Management
The field of hazardous materials management is evolving rapidly. Emerging technologies and regulatory changes are driving improvements in safety, efficiency, and environmental impact.
Emerging Technologies:
- Advanced Detection Tools: New technologies like drone-based inspections and real-time air quality monitoring systems are making it easier to identify hazardous materials quickly and accurately.
- Innovative Remediation Techniques: Methods such as bioremediation and nanotechnology are being explored to clean up contaminated sites more effectively and sustainably.
Regulatory Changes:
- Stricter Standards: As our understanding of the health impacts of hazardous materials grows, regulations are becoming more stringent. Keeping up with these changes is crucial for compliance and safety.
- Global Alignment: There is a trend towards harmonizing hazardous materials regulations globally, making it easier for multinational companies to manage compliance.
Industry Standards:
- LEED and RCRA Guidelines: Following guidelines from LEED Green and the Resource Conservation and Recovery Act (RCRA) helps minimize waste and promote sustainable practices.
- ISO Certifications: Adhering to ISO standards for environmental management ensures that companies are following best practices in hazardous materials management.
Importance of Professional Expertise
When it comes to managing hazardous building materials, the role of certified professionals cannot be overstated. Their expertise ensures that all aspects of identification, removal, and disposal are handled safely and in compliance with regulations.
Certified Professionals:
- Accredited Teams: Our team members are accredited and certified in various fields, including toxicology, environmental engineering, and industrial hygiene. This ensures that all assessments and remediation efforts are conducted to the highest standards.
- Comprehensive Solutions: From initial assessment to final remediation, our experts provide end-to-end solutions custom to your specific needs.
Best Practices:
- Continuous Improvement: At Omega Environmental Services, we are committed to continuous improvement. We stay updated with the latest industry trends and technologies to offer the most effective solutions.
- Proactive Management: Dealing with hazardous materials proactively helps avoid unexpected costs, delays, and health risks. Our comprehensive assessments and management plans ensure that all potential hazards are addressed before they become problems.
By understanding the future trends in hazardous materials management and the importance of professional expertise, you can make informed decisions that protect both your project and the environment.
For more information on how Omega Environmental Services can help you with your hazardous building materials assessment, click here to contact us or arrange a site visit.
By partnering with Omega Environmental Services, you can ensure that your project is safe, compliant, and successful. Our accredited teams are ready to provide comprehensive solutions custom to your needs.